Genuine PASCO® parts when you need them
Every PASCO® system uses components with standard industry part numbers that we engineer and manufacture in-house. That’s why we stock parts at reasonable prices, ship stocked parts same-day and make sure you talk to someone who knows your exact system when you call.
USA-MADE PASCO® PARTS
1,200+ PARTS STOCKED
Finding and waiting for parts shouldn’t slow down maintenance. We keep original manufacturer part numbers and stock 1,200+ components ready to ship same-day, with quotes in under an hour. Critical spares on hand before you need them.
ESTABLISHED VENDOR NETWORK
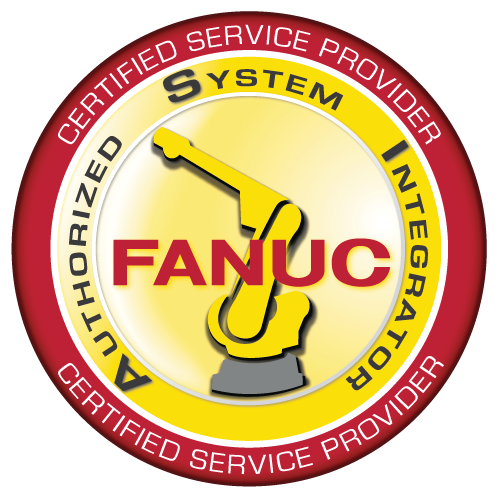
FANUC CERTIFIED INTEGRATOR
There are very few FANUC Certified Servicing Integrators. Why? It’s the highest level of factory certification. The path to certification is long, costly and demanding. And what does it mean? As a Certified Servicing Integrator, PASCO® offers the exact same level of knowledge and capability as FANUC factory technicians, which includes the ability to provide factory authorized warranty service.
Service done right
Most companies treat service as an afterthought – we continually invest in making quality service our advantage. That means 24-hour on-site response for down production, remote diagnostics that start immediately and real humans who answer within three rings. Simple as that.
PREVENT & PREDICT
Regular system checks catch small issues before they become line stoppages. Remote monitoring means fast diagnosis without travel time. We spot maintenance needs early and arrive with the right parts to keep your system running. That’s how we prevent downtime before it starts.
ISSUE MANAGEMENT
Our tech starts diagnostics immediately when you call. We solve it remotely when possible to save you downtime and cost. When we need to be there, we’re on site within 24 hours if your line is down. Because quick response only matters if we solve the problem.
NO MACHINE LEFT BEHIND
Age doesn’t make your system obsolete. Our engineers maintain detailed records of every build, which means we can repair, retrofit or replace any component today or ten years from now. That’s the OEM commitment we make to every customer.