A single automated palletizing cell can reduce labor costs for the production line by up to 50% while boosting line throughput by more than 35% within months of installation. Robotic palletizing uses industrial robots, conveyors and custom end-of-arm tooling to stack cases, bags, pails and beyond onto pallets with consistent speed and placement.
In this guide, we’ll cover:
- The key benefits driving ROI, safety and quality improvements
- The varieties of palletizing robots from six-axis articulated arms to collaborative cobots
- How custom end-of-arm tooling (EOAT) tailors each system to your product mix
- The steps for seamless integration with upstream and downstream equipment and software
- How PASCO®’s five decades of automation expertise ensures system performance and lifecycle support
What are the key benefits of robotic palletizing for manufacturers?
Robotic palletizing delivers a combination of continuous operation, precise handling and programmable versatility that enables end-of-line packaging to be a lean, error-proof process.
By replacing manual stacking with automated systems engineered for harsh environments, manufacturers gain measurable improvements in operational efficiency, employee safety and product quality, all while reducing labor costs.
How does robotic palletizing increase efficiency and throughput?
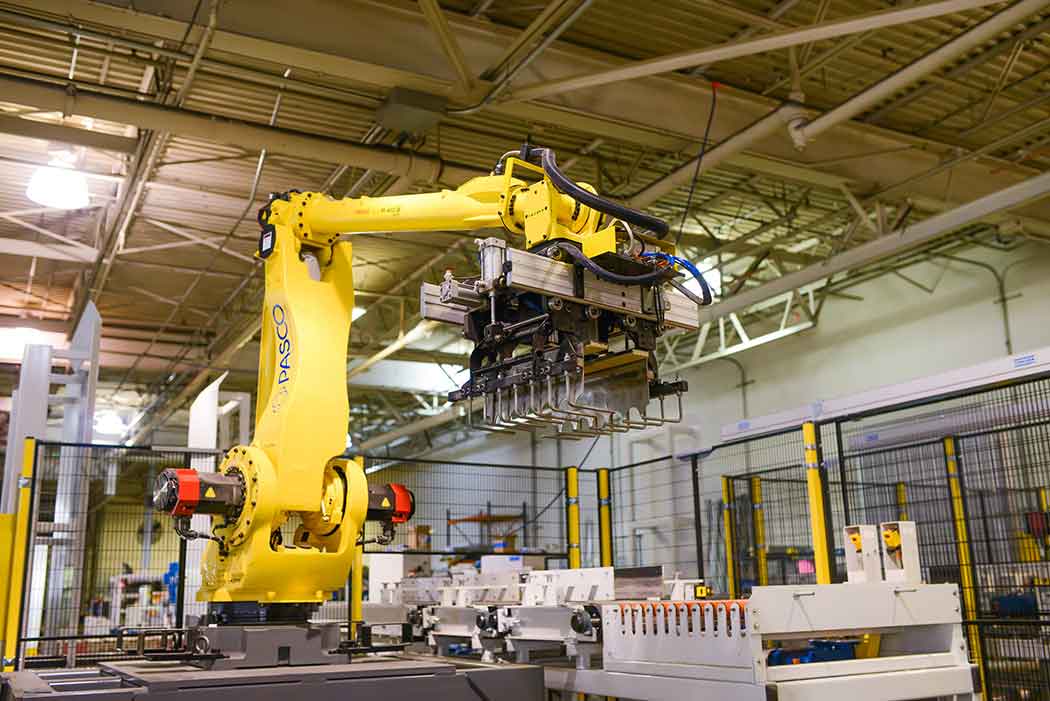
Robotic palletizers operate around the clock at consistent cycle times, eliminating the variability caused by shift changes or fatigue. Modern robots can complete up to 20 pallet patterns per minute, reducing downtime and ramp-up delays.
These systems automate pallet dispensing, pattern changeover and pallet removal without manual intervention.
Robotic palletizing ROI
Automated palletizing can significantly reduce labor costs and boost line throughput. Studies show that companies can see a return on investment within 2-3 years due to labor savings and increased efficiency.
This research supports the article’s claims about the financial benefits and efficiency gains of implementing robotic palletizing systems.
In what ways does robotic palletizing reduce labor costs?
Automated palletizing systems relieve labor from repetitive, ergonomically taxing tasks and allow redeployment to higher-value functions. Over a five-year period, companies often see a return on investment through labor savings that exceed initial capital outlay.
Below is an example cost comparison of manual versus robotic palletizing:
Robotic palletizing reduces annual labor expenses by nearly $330,000 while delivering payback within 24–36 months. These savings translate directly to improved profit margins and redeployment of skilled workers to system operation, maintenance or quality control.
How does robotic palletizing enhance workplace safety?
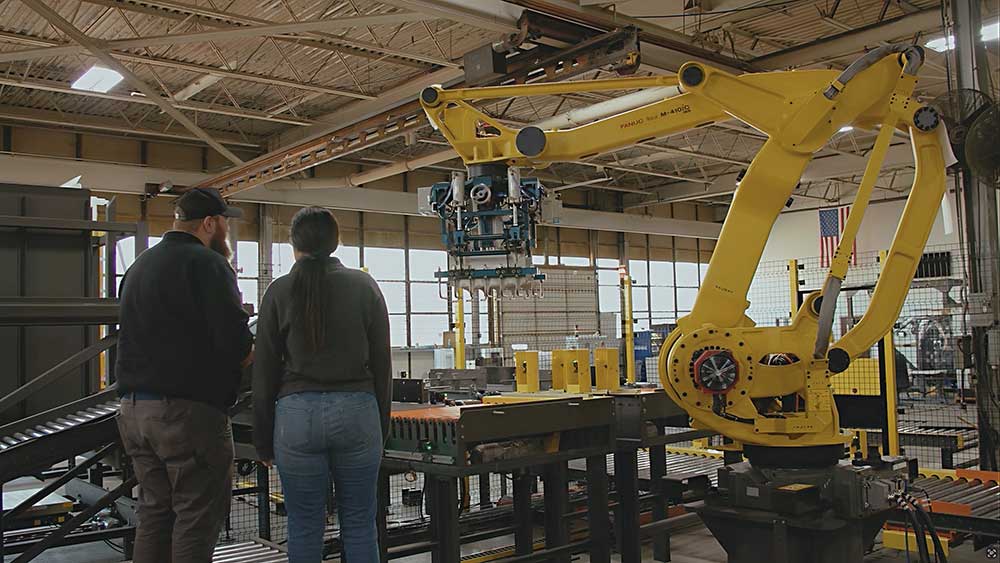
Robotic systems eliminate repetitive manual lifting of heavy loads, preventing musculoskeletal injuries and significantly reducing workers’ compensation claims. Integrated safety fences and light curtains create protective zones that isolate high-speed motions.
Our automated palletizing cells comply with OSHA, MSHA and ISO safety standards which cuts incident rates by more than 70% and creates a safer production environment for all plant personnel.
Why is accuracy and product quality improved with robotic palletizing?
Robotic palletizers have precision-programmed stacking patterns, eliminating human error in layer alignment, orientation and pallet alignment. Consistent end-of-arm tooling pressure and pick-and-place trajectories prevent product damage and minimize rework. Enhanced vision-system guidance further adapts to pallet height variances and product shape irregularities, improving load stability and reducing shrinkage across the supply chain.
What types of robotic palletizing systems does PASCO® offer?
PASCO® engineers custom robotic palletizers in a variety of configurations to match space constraints, payload requirements and throughput targets. We are an authorized integrator for FANUC, ABB, Kawasaki and Yaskawa, ensuring integration capabilities to match any existing production line.
How do collaborative robotic palletizers (cobots) work safely with humans?
Collaborative robots use force-limited joints, integrated safety sensors and responsive stopping algorithms to operate alongside workers without traditional guarding. Cobots handle much lighter payloads (often up to 20 kg) and are ideal for limited-throughput lines where human oversight or manual loading is required. Safe-speed settings and proximity detection create dynamic safety zones that pause robot motion if a worker enters the cell, enabling flexible, mixed-mode operations.
How does end-of-arm tooling (EOAT) customize robotic palletizing?
End-of-arm tooling defines the connection between the robot and your product, making EOAT design critical to reliable pick-and-place performance. Our in-house tooling engineers design custom grippers and vacuum systems for bags for precise handling of boxes, bags, cases and pails, regardless of surface texture or fragility.
What are the different types of grippers used in palletizing?
- Vacuum grippers that maintain sealed pick on flat, rigid surfaces
- Mechanical clamp grippers for irregular cartons and pails
- Soft bag grippers designed to cradle flexible packaging without puncture
How are custom EOAT designs tailored for diverse product handling?
We analyze product dimensions, packaging types and environmental factors (e.g., moisture, dust) to engineer end-of-arm tooling for your operation. By being a true OEM, we design and manufacture tooling in-house, allowing us to solve unique production challenges.
How is robotic palletizing easily integrated into production lines?
A truly automated cell connects mechanical, electrical and PLCs. We design turnkey solutions that dictate product flow, data exchange and safety interlocks across the entire end-of-line.
As a proud division of Pasco Systems Corp, we partner with our sister-company, Versatech, to design, manufacture and install end-to-end systems.
How do robotic palletizers connect with upstream and downstream equipment?
By integrating conveyors, pallet dispensers, case sealers and more, the palletizing cell becomes a continuous production segment. Standardized I/O protocols and safety relays ensure synchronized start/stop commands.
For example, a pallet dispenser downstream of a wrap station can automatically feed pallets into the robot cell at preset intervals, eliminating manual pallet loading.
Why choose PASCO® for your robotic palletizing needs?
With nearing 50 years of industrial automation experience, PASCO® combines engineering know-how, in-house manufacturing and 24/7 lifecycle support to deliver palletizing and end-of-line automation systems.
What experience and reliability does PASCO® bring to automation?
PASCO® has engineered thousands of custom robotic cells since 1976, solving complex handling challenges in food & beverage, chemicals, ice, building products and other production environments. A dedicated in-house fabrication shop and a team of seasoned field service technicians ensure rapid response to installation, commissioning and lifecycle support needs.
Which leading robot brands does PASCO® integrate with?
- FANUC
- ABB
- Kawasaki
- Yaskawa
What are the most common questions about robotic palletizing?
Manufacturers frequently evaluate cost, system types, operational principles, industry fit, efficiency impact and integration scope when considering a palletizing cell.
How much does a robotic palletizer cost?
System pricing ranges drastically depending on the application, but systems start typically in the $300,000 range. Final cost depends on product or packaging type, cycle rate, integration complexity and required safety features. Contact our automation experts for a tailored quote that factors in your unique application and ROI goals.
What are the main types of robotic palletizers?
Robotic palletizers fall into three primary categories: articulated arms with six or more axes, collaborative cobots designed for human-robot work cells, and gantry-style robots for high-speed, overhead stacking. Each type offers different benefits in reach, payload and footprint.
How does a robotic palletizer work?
A robotic palletizer picks products from a conveyor using EOAT, aligns them according to a programmed pallet pattern and places each layer onto a pallet. Integrated features, like vision, slip sheet placement, pallet orienting and more, ensure consistent pick reliability and accurate stacking across diverse packaging types.
Which industries benefit most from robotic palletizing?
Food and beverage, ice, pharmaceuticals, consumer goods, feed and seed, chemical products and building materials industries gain the greatest advantage from robotic palletizing due to high volume, repetitive packaging, strict quality requirements and labor-intensive processes.
Can robotic palletizers be integrated with existing systems?
Yes, modern palletizing robots interface with legacy conveyors, PLCs and warehouse management systems through standard protocols (Ethernet/IP, ProfiNet). This enables phased automation upgrades without complete line overhauls.
Over five decades, PASCO® has honed best-practice methodologies and built proprietary tooling to ensure every robotic palletizer operates reliably in the harshest environments.
By combining leading robot brands with in-house engineering and 24/7 field service, PASCO® transforms manual palletizing bottlenecks into automated high-performance cells that deliver fast ROI and sustained productivity gains.
Ready to elevate your end-of-line automation? Request a custom palletizing system quote from PASCO® today and discover how automation can optimize efficiency, enhance safety and maximize your cap-ex.